В данной статье расскажем о передовом решении для оптической инспекции операций поверхностного монтажа FLEX:Смарт-АОИ. Ключевой задачей этого комплексного решения является помощь производствам электроники в обеспечении высокого качества продукции с минимальными сопутствующими затратами.
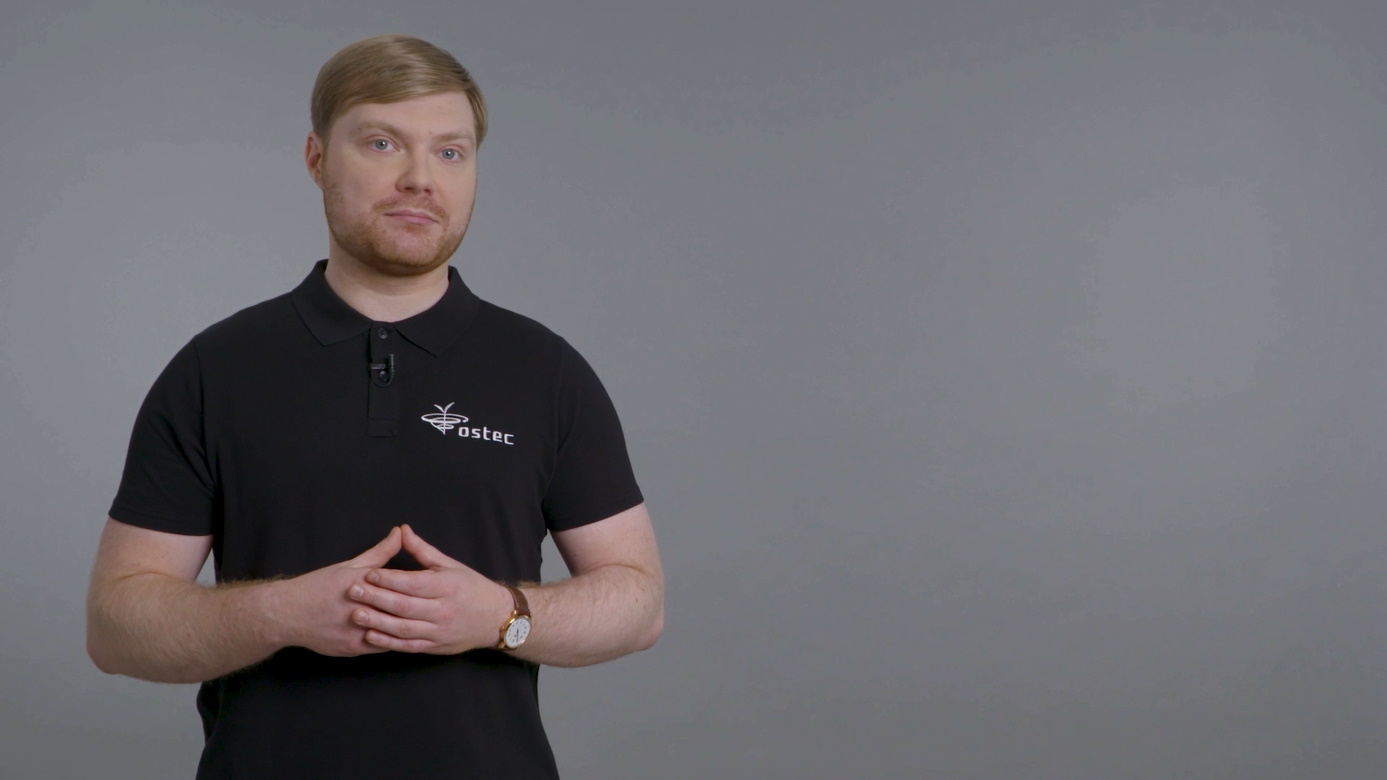
О решении
FLEX:Смарт-АОИ
Анализ опыта различных отечественных предприятий показывает, что есть много сложностей в вопросах автоматического контроля качества. Наиболее частые.
- Несмотря на автоматизацию, роль человека и трудозатраты на «ручной» контроль остаются существенными. Сложность изделий растет, а чем сложнее изделие, тем больше объем ложных срабатываний, как следствие – растет объем «ручных» проверок контролером.
- Большая часть дефектов, возникающих при поверхностном монтаже, связана с качеством нанесения паяльной пасты. Инспекция таких дефектов после этапа установки компонентов далеко не всегда обнаруживает брак, а в случае обнаружения дефектов на этом этапе стоимость ремонта обходится дороже, чем при отбраковке сразу после трафаретного принтера.
- Сложность и трудоемкость программирования инспекционного оборудования. Зачастую описание и внесение необходимых параметров осуществляется специалистом «вручную», с широким простором для творчества в определении критериев допустимого качества.
Для устранения этих сложностей команда Остека разработала комплексное решение для оптического контроля операций поверхностного монтажа, позволяющее обеспечить максимально возможный уровень автоматизации и свести к минимуму негативное влияние человеческого фактора.
Решение FLEX:Смарт-АОИ состоит из следующих элементов:
- Программное обеспечение подготовки рабочих программ
- Система автоматической инспекции нанесения паяльной пасты
- Система автоматической инспекции спаянных печатных узлов
- Программное обеспечение анализа результатов инспекции и визуализации
- Комплекс услуг поддержки в вопросах обеспечения качества
Расскажем о ключевых особенностях решения.
Подготовка рабочих программ
Традиционно подготовка рабочих программ для инспекционного оборудования является сложным и труднозатратным процессом, ведь программирование систем требует от специалиста высокой квалификации и глубокого знания механизма работы оборудования. Ему требуется описать сотни различных параметров, определяющих стабильность процесса контроля и достоверность его результатов. Любая ошибка чревата снижением эффективности инспекции, пропуском дефектов или ростом ложных срабатываний.
Процесс подготовки рабочих программ для систем оптического контроля максимально автоматизирован и существенно сократил время подготовки программ, повысив их качество и сведя влияние человеческого фактора к минимуму.
Как это работает?
В подавляющем большинстве случаев предприятие использует типовую номенклатуру компонентов, по которой в мире накоплен огромный практический опыт. Всего существует несколько тысяч типов корпусов компонентов. Инженеры вендора аккумулировали мировой опыт инспекции нескольких типовых компонентов и проанализировали необходимые параметры работы оборудования для обеспечения достоверной инспекции с учетом требований технологических стандартов, в частности, IPC-610.
Все результаты проделанной работы загружены в библиотеку программного обеспечения.
Благодаря этому при подготовке рабочих программ система определяет тип компонента и с учетом «оцифрованного мирового опыта» автоматически определяет оптимальные параметры инспекции.
При этом, разумеется, учитываются требования стандарта IPC-610 и класс изделия. Пользователю достаточно указать нужный класс, а все остальное программное обеспечение сделает автоматически.
Конечно, какая-то часть компонентов может быть «экзотической», и по ней потребуется ручная настройка, однако в среднем 90-95 % компонентов программируются автоматически.
Отдельно стоит отметить удобный и интуитивно понятный графический интерфейс пользователя, обеспечивающий качественные условия работы операторов установок.
Автоматическая инспекция качества нанесения пасты и пайки
В решении FLEX:Смарт-АОИ используются две новейшие модели систем инспекции нанесения пасты и пайки, способные решать современные актуальные задачи, а также длительно эксплуатироваться без морального устаревания.
Обе системы построены на одной платформе и оптимальным образом сбалансированы по техническим возможностям для совместного использования в составе одной линии.
Каждый автомат оснащен четырьмя проекторами, позволяющими получать высококачественные изображения для трехмерной реконструкции. То есть мы получаем качественную 3D-инспекцию с минимальным риском слепых зон и «шумов».
Разрешение инспекции можно изменять в диапазоне от 8 до 15 микрон, что обеспечивает гибкость в решении различных технологических задач.
Автоматическая верификация с использованием искусственного интеллекта
Важным этапом является анализ результатов инспекции. После проверки и выхода из линии часть плат автоматически помечается как подозрительные, то есть с высокой вероятностью содержащие дефекты.
Традиционно все такие платы проходят визуальную проверку контролером. И уже человек принимает решение о том, является ли дефект настоящим, или произошло ложное срабатывание.
Борьба за уменьшение доли ложных срабатываний является одним из приоритетных направлений в развитии инспекционного оборудования. Дело в том, что ложные срабатывания, безусловно, увеличивают нагрузку на персонал, а также вовлекают человека в процесс принятия окончательного решения о качестве. К сожалению, на текущем этапе развития технологий оптической инспекции полностью исключить ложные срабатывания невозможно, поэтому при высокой сложности изделий, широкой номенклатуре и больших объемах производства объем работы контролеров остается высоким.
Специалисты вендора совершили качественный прорыв в решении проблемы высоких трудозатрат специалистов отдела контроля. Это удалось сделать за счет применения технологий искусственного интеллекта и нейронных сетей, которые активно применяются в решении задач оценки и классификации изображения. В результате такой обработки приблизительно 70 % подозрительных плат проходят автоматическую верификацию без участия контролера. То есть на ручной контроль идет примерно в 3 раза меньше плат, что позволяет одновременно снизить затраты на персонал и влияние человеческого фактора.
Сбор и анализ статистики
Вся полученная статистика по результатам инспекции собирается в программном комплексе V-ONE. Полученные данные в удобной и наглядной форме могут быть выведены на экраны для оперативного мониторинга уровня качества и статистического анализа.
V-ONE позволяет собирать информацию со всего инспекционного оборудования, в том числе с систем рентгеновского и роботизированного контроля независимо от количества линий.
Комплекс FLEX:Смарт-АОИ позволяет обеспечить высокую эффективность инспекции и управления качеством на самом современном уровне. Решение может быть встроено как в новую линию поверхностного монтажа, так и в уже существующую на производстве.
В состав комплекса включен набор услуг поддержки в вопросах внедрения инспекционных систем и специализированного программного обеспечения. Это важно для полноценного обучения профильного персонала и успешного повышения качества продукции.
Специалисты Остека будут рады ответить на любые вопросы и помочь подобрать наиболее эффективное решение ваших производственных задач.